Hybrids of additive manufacturing and CNC machining can shorten tooling turnaround times.
Development of additive toolmaking processes (aka 3D printing) have opened new possibilities for geometries that cannot be achieved with traditional machining of steel blanks. These geometries include tools with conformal cooling channels, which can make injection molding operations more efficient and prevent defects due to uneven cooling. Approaches differ both in their method of forming the shape of the tooling and the method of solidifying the material. Products
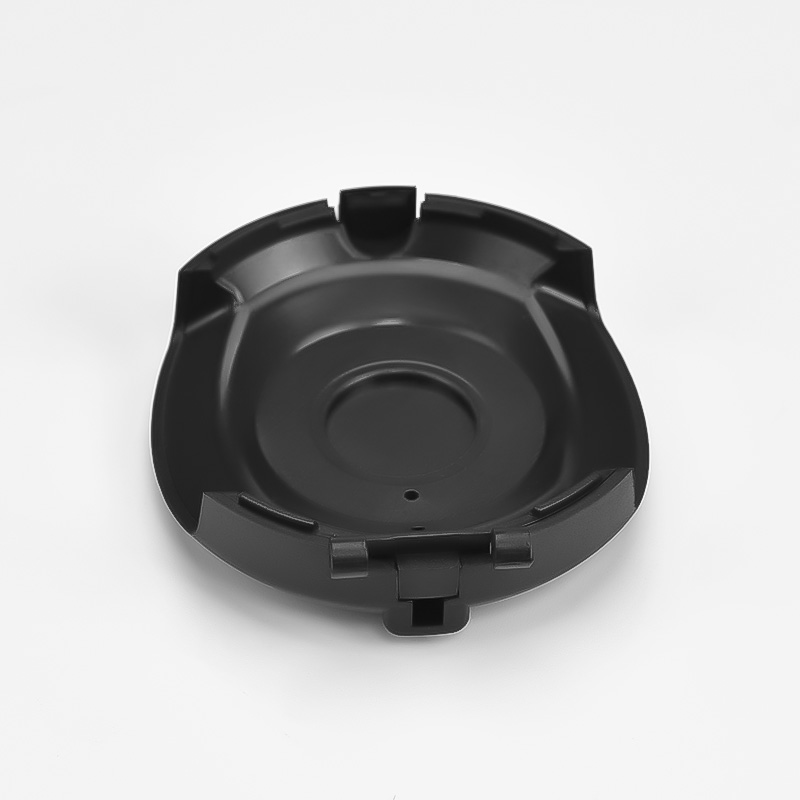
The additive manufacturing (AM) approach in widest use is powder bed fusion, in which an energy source, either a laser or electron beam, forms the geometry by selectively heating a layer of metal powder to its melting temperature. Layer by layer, the tool is built by fusing the powder only where necessary. Powder bed fusion has found a niche in complex applications in the aerospace, healthcare, and automotive sectors, where gains in efficiency and quality justify the expense and complexity of the laser or electron beam system.
A competing process, binder jetting, forms the desired shape by selectively depositing a layer of adhesive binder onto a bed of powdered metal. After each layer, the platform is lowered and an additional layer of powder is applied, followed by another layer of binder. When printing is complete, the part is transferred to a furnace for sintering, thus eliminating the need for a laser or electron beam. However, the part shrinks significantly during the densification process, as media and binding materials are vaporized. Controlling dimensions is complicated by changes that can be as large as 20% to 25%. Shrinkage can be especially problematic at transitions between thick and thin regions, where residual stress can be imparted to the tool and may even cause breakage.
Additive techniques for making molds and inserts require post-processing to remove witness lines and give the tool its final shape and finish necessary for molding plastic. Hybrid systems reduce this work by incorporating subtractive machining steps into the build process. By reducing the amount of post-processing work, this approach frees skilled tool makers to work on a greater number of projects by reducing the time spent per tool. This could be especially important given reported shortages of workers with highly specialized skills.
One hybrid approach aimed at minimizing the dimensional contraction problem and reducing postprocessing time has been developed by Mantle, Inc. of California. Mantle provides solutions to injection molders and mold makers based on its Trueshape technology, which incorporates fused deposition modeling and CNC machining into one system. The company’s P-200 printer was launched last September.
Mantle’s process begins with a digital model and a flowable metal paste. The paste consists of steel particles suspended in a solvent with a binding material. Steels available at present include the widely used tool steel H13 and P2X, which mimics the properties of P20 tool steel.
Tooling insert printed by Mantle for Tessy Plastics. (Photos: Mantle, Inc.)
Most of the workflow is hands-off. The printer builds the part up gradually, laying down paste layer by layer, drying it, and periodically removing material with an integrated CNC machine. Placing this step before sintering boosts efficiency by enabling the system to cut this material away while it is still soft. The machine can run for hours or days without operator intervention, guided by software and the digital model of the geometry.
When the printing is complete, the operator moves the tool to the furnace for sintering. It is heated just enough for the individual particles to fuse together, and the binder is removed, leaving a tool that is now solid steel, ready for final finishing.
Mantle’s strategy to counter the effects of densification has been twofold: prevention and prediction. The process is designed to reduce the dimensional effects of densification, from 20-25% to less than 9%.
“The challenge has always been predicting what is going to come out of the furnace at the end. We’ve spent the last seven years focusing on being able to predict that outcome,” says Ted Sorom, co-founder and CEO at Mantle.
The years of development work have allowed Mantle’s process to achieve tolerances as tight as 0.001 in and smoothness of 2-3 microns Ra, meaning that the required finishing is relatively minor compared with what is needed for other methods. According to Mantle, the process has saved its customers up to 70% of production time when compared with more conventional subtractive machining.
The resulting tool is suitable for production and performance is comparable to a traditionally made steel tool from the same material. In the case of H13, the material is the same chemically. The lifespan of printed tools in production is estimated to be within 10% of that for traditionally built tools. Mantle-printed tool inserts in use at injection molder Tessy Plastics, have reportedly run 1.65 million cycles and counting.
In February, Mantle released case studies describing additional success stories from injection molding customers. Westec Plastics Corporation used Mantle technology to produce a prototype tool for validating a medical diagnostic part. Grinding and EDM work to finish the 3D printed inserts required only 10 hr, compared with 35 to 40 hr for traditional techniques.
3D-printed tool for a medical diagnostic part. The use of tool steel enables production of parts that are appropriate for validation.
For Nicolet Plastics, Mantle printed a cavity and core inserts for molding a 35% glass-filled part with a lead time of only two weeks, something that would otherwise take an estimated six weeks. The printed tooling reduced hands-on toolmaking time by more than 90%.
Mantle’s P-200 printer. Photo Credit: Mantle
In May, Mantle was recognized with the SME’s AM Startup Award for its Trueshape technology and P2X material. The award, announced at Rapid+TCT, recognizes a company that has developed “a new technology or application solving an existing problem or unique approach.”
Automated, flexible, and efficient, this hybrid-AM strategy could become the default means for making injection mold tooling in the future. “There’s no question, in my mind, that it will be either Mantle’s technology or a similar technology that incorporates additive and subtractive processes,” says Sorom.
What’s the return on investing in a new mold with conformal cooling to boost productivity? Will it pay for itself? How soon? Here’s a case study on how to answer those questions.
Questioning several “rules of thumb” about venting injection molds.
Gate size and shape—unlike gate location—don’t often get the attention they deserve. Many common assumptions about gate geometry deserve to be challenged
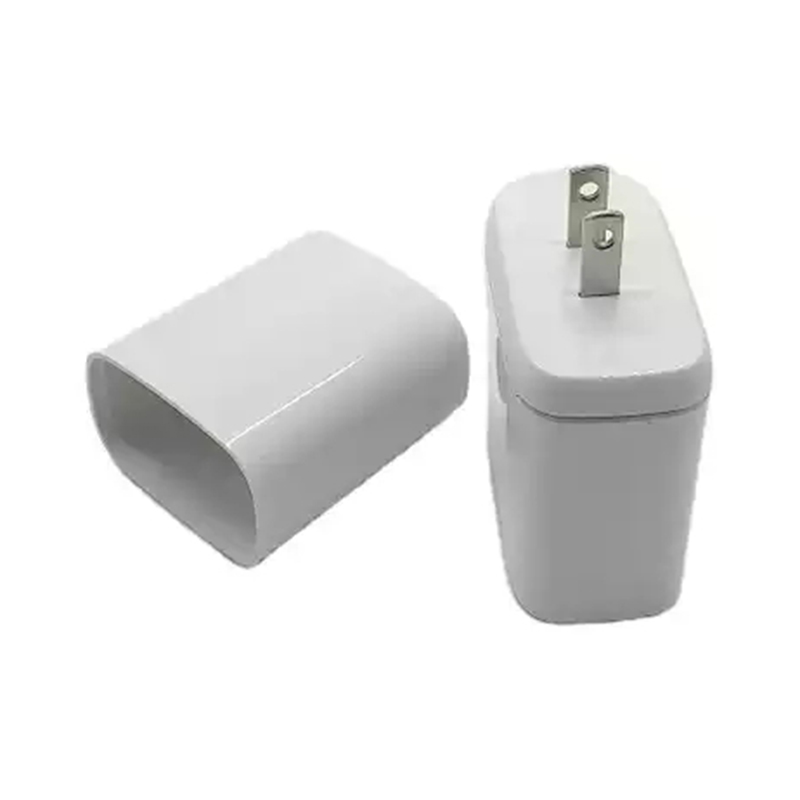
Electric Cup Warmer For Desk © 2023 Gardner Business Media, Inc. Privacy Policy [Log On]